Приварка фланца к трубе плоская, сквозная и воротниковая
Фланцевое соединение довольно часто используют вместо обычной сварки, а тем более на фитинг.
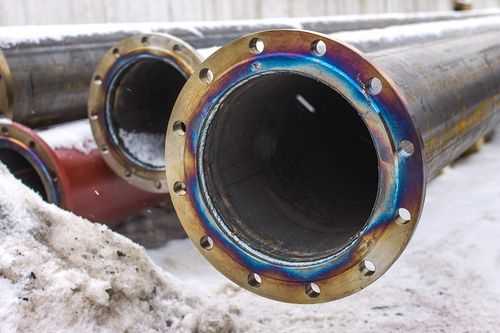
Фланцевое соединение
Фланец гарантирует не менее прочное и герметичное соединение, но при этом разъемное, чтопозволяет в любой момент демонтировать часть трубопровода для ремонта, например, или присоединения дополнительных секторов.
Классификация изделий
Общее строение детали представляет собой кольцои пластину с отверстиями по краю. Чтобы обеспечить герметичность между элементами, устанавливают еще и прокладку изрезины в соответствии с назначением трубопровода – кислотостойкой, термостойкой. Соединяют кольцо и пластину с помощью крепежа – болтов с гайками или шпилек.
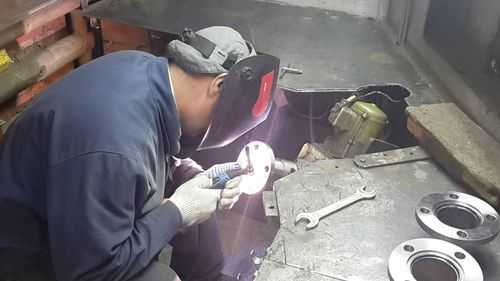
Сварка фланцев
По ГОСТ выделяют несколько разных видов фланцев. По чертежам отличия их хорошо заметны.
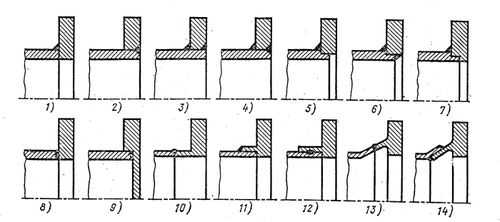
Виды сваривания фланцев
Соответственно, и приварка деталей к трубопроводу производится несколько по-разному.
- Воротниковый – характерным признаком является приварная горловина в виде конического концентратора. Такая форма позволяет более равномерно распределять давление. Воротниковая модель предназначена для коммуникаций с высоким давлением и высокой температурой носителя. Приваривается сплошным или V-швом.
- Раструбной – используется на трубах с малым диаметром, работающих под большим давлением. Минус изделия – некоторая нестойкость к коррозии. Приварка раструбной детали производится с внешней стороны угловым швом. Нужно сохранять люфт в 1,6 м, чтобы нейтрализовать эффект теплового расширения.
- Сквозной – или свободно вращающийся. Приварка сквозной трубы к фланцу по ГОСТ не производится, так как сквозной вариант применяется специально для того, чтобы деталь можно было заменить по мере необходимости. На фото – сквозное фланцевое соединение.
- Глухой – плоский диск с отверстиями. Это приспособление необходимо для заглушки концов трубопровода. Элемент неразборной, однако он только закрепляется, а не сваривается.
- Плоский – кольцо и пластина одинакового размера. Приварка плоского фланца к трубе заключается в креплении кольца, в то время как пластина остается свободного вращающейся. Он выдерживает давление до 2,5 МПа.
- Накидной – для его использования кромки труб должны быть идеально ровными, так что он не настолько универсален, как воротниковые модели. Накидной приваривается угловыми швами с внешней и с внутренней стороны.
- Резьбовый – используется на трубопроводах небольшого диаметра, где возможно сделать резьбу. Сварка при его установке используется крайне редко.
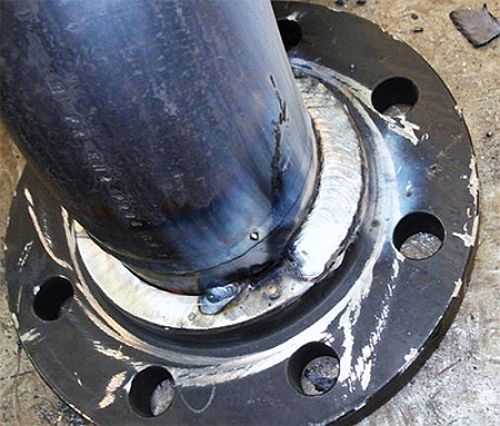
Наружняя приварка фланца
Расценки на изделия заметно отличаются. Однако стоимость переделяетсяскорее размерами пластин, а не их конструкцией, и весом, конечно же. Согласно ГОСТ изготавливаются они из углеродистой, легированной или нержавеющей стали, а такжековкого чугуна. Расценки на металл и определяют стоимость приспособлений.
Приварка фланца к трубе по ГОСТ
Технология сварки в принципе одинакова, за исключением крепления патрубков. Однако необходимо учитывать и сложность конструкции – рекомендуется уточнять чертежи, и соответствие требованиям по креплению.
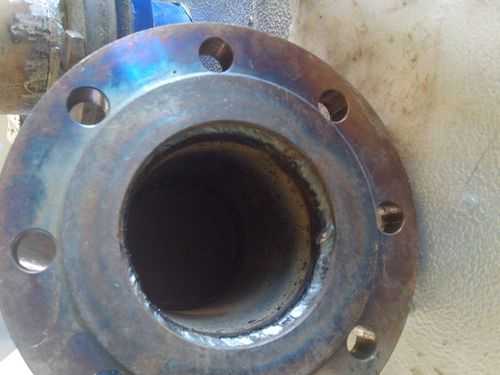
Внутренняя приварка фланца
В большинстве случаев необходимо сохранение зазора в стыке. Если люфт не нужен, допускается техника сварки в лодочку. Если люфт должен быть большим – более 4–5 мм, изделие приваривают угловыми швами. Все это, естественно, влияет на расценки.
Размеры шва зависят от трубопровода. Ширина внутреннего шва обычно равна толщине стенки, высота – от 0,5 до 1 см, что определяется сечением трубопровода. Внешний шов требует большего наплавления металла, поэтому он несколько несимметричен.
Приварка производится с 2 сторон: сначала с наружной, а затем, для уплотнения шва – с внутренней. Такой метод более всего подходит для плоских фланцевых деталей. Сварка с одной стороны осуществляется, если изделие приваривается встык, как в случае с воротниковым фланцем.
Приспособление для приварки фланцев к трубам подходит не всякое. Обычно рекомендуется аппарат Лисицына и Бондаренко. При сварке электрод здесь остается неподвижным, а проворачивается трубопровод.
На видео процесс сварки рассматривается более подробно.
trubygid.ru
ГОСТ 16037-80* «Соединения сварные стальных трубопроводов. Основные типы, конструктивные элементы и размеры»
ГОСУДАРСТВЕННЫЙ СТАНДАРТ СОЮЗА ССР
СОЕДИНЕНИЯ СВАРНЫЕ СТАЛЬНЫХ ТРУБОПРОВОДОВ
Основные типы, конструктивные элементы и размеры
ГОСТ 16037-80
СОЕДИНЕНИЯ СВАРНЫЕ СТАЛЬНЫХ ТРУБОПРОВОДОВ Основные типы, конструктивные элементы и размеры Welded joints in steel pipelines. Main types, design elements and dimensions |
ГОСТ |
Срок действия с 01.07.81
до 01.07.90
1. Настоящий стандарт распространяется на сварные соединения трубопроводов из сталей и устанавливает основные типы, конструктивные элементы и размеры сварных соединений труб с трубами и арматурой.
Стандарт не распространяется на сварные соединения, применяемые для изготовления самих труб из листового или полосового материала.
Требования настоящего стандарта являются обязательными.
2. В стандарте приняты следующие обозначения способов сварки:
ЗП – дуговая сварка в защитном газе плавящимся электродом;
ЗН – дуговая сварка в защитном газе неплавящимся электродом;
Р - ручная дуговая сварка;
Ф - дуговая сварка под флюсом;
Г - газовая сварка.
Для конструктивных элементов труб, арматуры и сварных соединений приняты следующие обозначения:
s, s1 – толщины стенок свариваемых деталей;
b – зазор между кромками свариваемых деталей после прихватки;
e – ширина сварного шва;
g – выпуклость сварного шва;
d – толщина подкладного кольца;
а - толщина шва;
с - притупление кромки;
В - ширина нахлестки;
l – длина муфты;
K – катет углового шва;
K1 – катет углового шва со стороны разъема фланца;
Dn
f – фаска фланца.
1, 2. (Измененная редакция, Изм. № 1).
3. Основные типы сварных соединений должны соответствовать указанным в табл. 1.
4. Конструктивные элементы и их размеры должны соответствовать указанным в табл. 2-33.
Для угловых швов в таблицах приведен расчетный катет.
files.stroyinf.ru
Сварка фланцев – Svarcom
В современном мире сварка фланцев весьма распространенное явление. Фланец – это деталь круглой или квадратной формы с отверстиями для крепления отдельных частей трубо -, газо-, нефтепроводов, строительных конструкций большой длины.
Для чего предназначен фланец?
В основном фланцы предназначаются для формирования быстросъемных фланцевых соединений на трубах. В отличии от сварки такая конструкция обеспечивает возможность быстрого соединения или съема отдельных частей трубопровода, например, для проверки состоянии трубы на отдельных участках, установки кранов, датчиков, для возможности слива воды или для присоединения оборудования (тот же теплообменник). Фланцы навариваются на окончания труб и соединяют между собой болтами, шпильками в комплекте с ответным фланцем. Между ними обязательно ставятся прокладки из резины или других материалов.
Фланцы используются в разных отраслях промышленности и коммунального хозяйства для герметичного подключения определенного участка трубопровода к различным технологическим аппаратам и устройствам с целью подвода и отвода сред, а также для стыковки между собой отдельных участков трубы.
Классификация. Типы фланцев
Фланцы в разных странах изготавливаются по стандартам, соответствующим конкретным нормам, принятым в этих странах. Это может быть ГОСТ (для Украины ДСТУ ISO 7005-2:2005 (ІSO 7005-2:1988, ІDT). Металеві фланці.)), DIN или ТУ. По форме выделяются круглые, квадратные. Можно выявить два существенных группы фланцев:
- для арматуры
- для сосудов и аппаратов.
Выделяются следующие наиболее часто применяемые виды фланцев:
Приварной фланец воротниковый, накидной, раструбный, свободно вращающийся, резьбовой, глухой фланец. Пройдемся кратко по каждому из них.
Воротниковый фланец
Имеют характерную приварную горловину в виде конического концентратора, плавно переходящего к трубной стенке. Она обеспечивает распределение давления подаваемых веществ через конусную ступицу. Используется для трубопроводов с высоким давлением или высокими/низкими температурами. Воротниковый фланец необходимо приваривать V-образным или сплошным швом.
Фланцевый патрубок
Чаще всего применяется для второстепенных задач как подложка фланца для недорогой отбортовки.
Раструбный фланец
Предназначены для малогабаритных труб с большим давлением. Их срок службы в два больше чем у проваренных накидных фланцев. К недостаткам относится возможность разрывов, подверженность коррозии.
Сварка раструбных фланцев производится только с внешней стороны угловым швом встык, при этом необходимо чтобы остался небольшой люфт примерно в 1,6 мм чтобы компенсировать эффект теплового расширения (на картинке обозначено «Х»).
Накидной фланец
Требуют ровных краев трубы при соединении. Их срок службы в два-три раза меньше чем у воротниковых фланцев. из-за Сварка накидных фланцев производится с внешней и внутренней стороны угловыми сварными швами. Чтобы не повредить во время сварки поверхность фланца необходимо чтобы был зазор в 3 мм между концом трубы и внутренней кромкой фланца.
Вращающийся фланец
Свободно вращается на трубе, не привариваются. Вращающийся фланец при необходимости можно легко снять и заменить. Могут крепиться противоположными болтовыми соединениями.
Глухой фланец
Являет собой диск плоской формы с отверстиями для шпилек, болтов. Предназначены для перекрытия концевых отверстий труб, трубопроводов. В сочетании с другими фланцами, соединение такого типа является разборным. Не сваривается.
Резьбовой фланец
Приваривается редко, используется для трубопроводной арматуры, а также труб небольшого диаметра с толщиной стенки, достаточной для нарезки резьбы. В редких случаях может быть сделан уплотняющий сварной шов.
Сварка фланцев — техника
Величина зазора в стыке или как часто его называют люфт часто определяет технику сварки. В общей сложности 7/10 всех стыков «внутренний диаметр фланца-труба» требуют наличия небольшого люфта. В случае когда зазор не требуется, используется техника в лодочку, так как она минимально подвержена затеканиям расплавленного металла и при этом кромки глубоко провариваются. Если люфт превышает 1.5 мм, для хорошей свариваемости применяется техника поперечных колебательных движений электрода под углом 30° к плоскости оси трубы.
Для зазора в 4-5мм, сварка ведется угловыми швами с большими катетами равными стандартной величине плюс высота зазора.
Ширина и высота шва зависят от размера трубы в поперечнике. Обратимся к примерам. Для внешнего шва необходимо большее количество наплавленного металла со стороны фланца. Таким образом шов немного не симметричен и его катет на трубе будет меньше. Ширина внутреннего шва в идеале должна соответствовать толщине трубы, но не более 0,7 см. Высота — от 0,5 до 1 см в зависимости от сечения трубы в поперечнике.
Сварка фланцев должна проводиться с двух сторон. Чтобы получить крепкое соединение необходимо сначала проварить с наружной, а после для уплотнения с внутренней стороны. Таким образом внутренний и наружный сварные швы очень прочно соединят две части сварного узла. Такая практика применима для плоских стальных фланцев. При этом в тех местах, где зазоры более 2,5 мм, для присадки используется электрод или сварочная проволока о 1.6-2.5 мм.
Сварка фланцев с двух сторон начинается сначала с внутренней стороны. После сравниваются неровности прихватки с внешней стороны, проводится зачистка и сварка в направлении слева- направо. Два прохода нужны только в том случае, если получается большой зазор.
Накладка сварного шва только с одной стороны применима для стальных фланцев, привариваемых встык, когда вплотную соединяются «воротник» фланца и торец трубы.
Сварка патрубков
Предварительно патрубок и фланец прихватывают с соблюдением всех углов. После сварной узел устанавливается на вращатель. Обрызгивается спреем против сварочных брызг и начинаем сварку.
Стандартно, согласно ГОСТу 16037-80 для труб с давлением от 10 до 25 кгс/см2 необходимо на фланце делать скосы .
Для приварки фланцев, патрубков рекомендуется использовать вращатели. Они дают возможность легко вращать, наклонять в нужное положение и приподнимать обрабатываемую деталь или кусок трубы. Таком образом можно без лишних усилий сваривать, шлифовать или даже красить объект
Необходимые меры предосторожности
Сварка фланцев требует внимания и соблюдения мер, способных уберечь сварщика от наиболее распространенных ошибок. Предварительно перед сваркой нужно зачистить и подготовить кромки. Соединяя воедино фланцевые соединения следите за тем, чтобы они были строго перпендикулярны к оси трубы. Допустимые отклонения могут быть до 1 % от наружного диаметра фланца, но не превышать 2 мм.
Чтобы проверить ровно ли приварен фланец (перпендикулярность, соосность) можно воспользоваться обычным или специально предназначенным угольником для фланцев.
При самостоятельной сборке узлов требуется учитывать длину болтов, толщину прокладки. Необходимо чтобы все головки болтов располагались с одной стороны, не были утоплены, а их окончания выступали на уровень трех шагов резьбы. Сварной шов и край трубы не должны быть выше уровня зеркала фланца.
Конец трубы, включая шов приварки фланца к трубе, не должен выступать за зеркало фланца. Отклонения линейных размеров собранных узлов не должны превышать ±3 мм при длине до 1 м и ±1 мм на каждый последующий метр.
Контроль качества сварных швов
Для проверки качества сварного шва чаще всего используют старый добрый внешний осмотр с замерами размеров при надобности. Убедитесь в том, что видимые дефекты отсутствуют:
- трещины,
- непровары,
- кратеры более 0,5 мм,
- прожоги,
- поры,
- шлаковые включения,
- значительные отклонения высоты или ширины шва,
- подрезы и наплывы в переходной зоне от основного металла к наплавленному.
Неразрушающие методы контроля: ультразвуковой, радиографический метод. Последний обязателен для контроля допускных стыков. Иногда металлографические исследования.
blog.svarcom.net
Сварка фланцев к трубе
Сварка фланцев
В современном мире сварка фланцев весьма распространенное явление. Фланец – это деталь круглой или квадратной формы с отверстиями для крепления отдельных частей трубо -, газо-, нефтепроводов, строительных конструкций большой длины.
Для чего предназначен фланец?
В основном фланцы предназначаются для формирования быстросъемных фланцевых соединений на трубах. В отличии от сварки такая конструкция обеспечивает возможность быстрого соединения или съема отдельных частей трубопровода, например, для проверки состоянии трубы на отдельных участках, установки кранов, датчиков, для возможности слива воды или для присоединения оборудования (тот же теплообменник). Фланцы навариваются на окончания труб и соединяют между собой болтами, шпильками в комплекте с ответным фланцем. Между ними обязательно ставятся прокладки из резины или других материалов.
Фланцы используются в разных отраслях промышленности и коммунального хозяйства для герметичного подключения определенного участка трубопровода к различным технологическим аппаратам и устройствам с целью подвода и отвода сред, а также для стыковки между собой отдельных участков трубы.
Классификация. Типы фланцев
Фланцы в разных странах изготавливаются по стандартам, соответствующим конкретным нормам, принятым в этих странах. Это может быть ГОСТ (для Украины ДСТУ ISO 7005-2:2005 (ІSO 7005-2:1988, ІDT). Металеві фланці.)), DIN или ТУ. По форме выделяются круглые, квадратные. Можно выявить два существенных группы фланцев:
- для арматуры
- для сосудов и аппаратов.
Выделяются следующие наиболее часто применяемые виды фланцев:
Приварной фланец воротниковый, накидной, раструбный, свободно вращающийся, резьбовой, глухой фланец. Пройдемся кратко по каждому из них.
Воротниковый фланец
Имеют характерную приварную горловину в виде конического концентратора, плавно переходящего к трубной стенке. Она обеспечивает распределение давления подаваемых веществ через конусную ступицу. Используется для трубопроводов с высоким давлением или высокими/низкими температурами. Воротниковый фланец необходимо приваривать V-образным или сплошным швом.
Фланцевый патрубок Чаще всего применяется для второстепенных задач как подложка фланца для недорогой отбортовки.
Раструбный фланец
Предназначены для малогабаритных труб с большим давлением. Их срок службы в два больше чем у проваренных накидных фланцев. К недостаткам относится возможность разрывов, подверженность коррозии.
Сварка раструбных фланцев производится только с внешней стороны угловым швом встык, при этом необходимо чтобы остался небольшой люфт примерно в 1,6 мм чтобы компенсировать эффект теплового расширения (на картинке обозначено «Х»).
Накидной фланец
Требуют ровных краев трубы при соединении. Их срок службы в два-три раза меньше чем у воротниковых фланцев. из-за Сварка накидных фланцев производится с внешней и внутренней стороны угловыми сварными швами. Чтобы не повредить во время сварки поверхность фланца необходимо чтобы был зазор в 3 мм между концом трубы и внутренней кромкой фланца.
Вращающийся фланец
Свободно вращается на трубе, не привариваются. Вращающийся фланец при необходимости можно легко снять и заменить. Могут крепиться противоположными болтовыми соединениями.
Глухой фланец
Являет собой диск плоской формы с отверстиями для шпилек, болтов. Предназначены для перекрытия концевых отверстий труб, трубопроводов. В сочетании с другими фланцами, соединение такого типа является разборным. Не сваривается.
Резьбовой фланец
Приваривается редко, используется для трубопроводной арматуры, а также труб небольшого диаметра с толщиной стенки, достаточной для нарезки резьбы. В редких случаях может быть сделан уплотняющий сварной шов.
Сварка фланцев — техника
Величина зазора в стыке или как часто его называют люфт часто определяет технику сварки. В общей сложности 7/10 всех стыков «внутренний диаметр фланца-труба» требуют наличия небольшого люфта. В случае когда зазор не требуется, используется техника в лодочку, так как она минимально подвержена затеканиям расплавленного металла и при этом кромки глубоко провариваются. Если люфт превышает 1.5 мм, для хорошей свариваемости применяется техника поперечных колебательных движений электрода под углом 30° к плоскости оси трубы.
Для зазора в 4-5мм, сварка ведется угловыми швами с большими катетами равными стандартной величине плюс высота зазора.
Ширина и высота шва зависят от размера трубы в поперечнике. Обратимся к примерам. Для внешнего шва необходимо большее количество наплавленного металла со стороны фланца. Таким образом шов немного не симметричен и его катет на трубе будет меньше. Ширина внутреннего шва в идеале должна соответствовать толщине трубы, но не более 0,7 см. Высота — от 0,5 до 1 см в зависимости от сечения трубы в поперечнике.
Сварка фланцев должна проводиться с двух сторон. Чтобы получить крепкое соединение необходимо сначала проварить с наружной, а после для уплотнения с внутренней стороны. Таким образом внутренний и наружный сварные швы очень прочно соединят две части сварного узла. Такая практика применима для плоских стальных фланцев. При этом в тех местах, где зазоры более 2,5 мм, для присадки используется электрод или сварочная проволока о 1.6-2.5 мм. Сварка фланцев с двух сторон начинается сначала с внутренней стороны. После сравниваются неровности прихватки с внешней стороны, проводится зачистка и сварка в направлении слева- направо. Два прохода нужны только в том случае, если получается большой зазор.
Накладка сварного шва только с одной стороны применима для стальных фланцев, привариваемых встык, когда вплотную соединяются «воротник» фланца и торец трубы.
Сварка патрубков
Предварительно патрубок и фланец прихватывают с соблюдением всех углов. После сварной узел устанавливается на вращатель. Обрызгивается спреем против сварочных брызг и начинаем сварку.
Стандартно, согласно ГОСТу 16037-80 для труб с давлением от 10 до 25 кгс/см2 необходимо на фланце делать скосы .
Для приварки фланцев, патрубков рекомендуется использовать вращатели. Они дают возможность легко вращать, наклонять в нужное положение и приподнимать обрабатываемую деталь или кусок трубы. Таком образом можно без лишних усилий сваривать, шлифовать или даже красить объект
Необходимые меры предосторожности
Сварка фланцев требует внимания и соблюдения мер, способных уберечь сварщика от наиболее распространенных ошибок. Предварительно перед сваркой нужно зачистить и подготовить кромки. Соединяя воедино фланцевые соединения следите за тем, чтобы они были строго перпендикулярны к оси трубы. Допустимые отклонения могут быть до 1 % от наружного диаметра фланца, но не превышать 2 мм.
Чтобы проверить ровно ли приварен фланец (перпендикулярность, соосность) можно воспользоваться обычным или специально предназначенным угольником для фланцев.
При самостоятельной сборке узлов требуется учитывать длину болтов, толщину прокладки. Необходимо чтобы все головки болтов располагались с одной стороны, не были утоплены, а их окончания выступали на уровень трех шагов резьбы. Сварной шов и край трубы не должны быть выше уровня зеркала фланца.
Конец трубы, включая шов приварки фланца к трубе, не должен выступать за зеркало фланца. Отклонения линейных размеров собранных узлов не должны превышать ±3 мм при длине до 1 м и ±1 мм на каждый последующий метр.
Контроль качества сварных швов
Для проверки качества сварного шва чаще всего используют старый добрый внешний осмотр с замерами размеров при надобности. Убедитесь в том, что видимые дефекты отсутствуют:
- трещины,
- непровары,
- кратеры более 0,5 мм,
- прожоги,
- поры,
- шлаковые включения,
- значительные отклонения высоты или ширины шва,
- подрезы и наплывы в переходной зоне от основного металла к наплавленному.
Неразрушающие методы контроля: ультразвуковой, радиографический метод. Последний обязателен для контроля допускных стыков. Иногда металлографические исследования.
blog.svarcom.net
Фланцы для трубопроводов: применение сварки помогает соединить трубы
Фланцы широко применяются для надежного и герметичного соединения труб, валов, различных вращающихся деталей и компонентов аппаратов и машин. Самым распространенным способом установки фланца на трубу является приварной.
Типы фланцев
В соответствии с требованиями американской системы стандартов ANSI/ASME разделяют такие основные типы фланцев:
- с шейкой для приварки Welding Neck;
- сквозные Slip-on;
- нарезные или резьбовые Threaded flanges;
- приварные внахлест (свободновращающиеся) Lap Joint;
- приварные с впадиной под сварку Socket-welding;
- фланцевые заглушки Blind flanges.
Способы приварки фланцев
Существует всего два способа сварки фланца.
- Приварка встык. При этом способе диск сваривается с трубой по всему периметру после состыковки.
- Приварка надетого на трубу приварного диска. В таком случае сварка производится по наружной и внутренней поверхности кольца.
Оба способа приварки фланца являются довольно сложными. В процессе сварки используются все типы сварочных швов: горизонтальные, вертикальные и потолочные. Сварочные работы с участием фланцевых соединений требуют высокой квалификации сварщика.
Особенности процесса сборки фланцевого соединения
Фланцевое соединение является слабым и уязвимым местом в трубопроводе.
Перекосы плоскостей при установке колец могут привести к образованию дефектов, нарушению герметичности узла и, в конечном счете, создать аварийную ситуацию на магистрали.
Поэтому, при сборке фланцевых соединений важно обеспечить:
- перпендикулярность кольца к основной трубе;
- совпадение осей болтовых отверстий относительно оси симметрии.
Перпендикулярность сборки фланцевых соединений контролируют при помощи специального контрольного угольника и щупа. Отсутствие смещения осей отверстий выявляется уровнем и отвесом. Допустимое отклонение от перпендикулярности кольца по отношению к трубе не должно превышать 0,2 мм на 100 мм диаметра трубы.
Смещение оси отверстий фланцев относительно оси симметрии основной трубы должно быть менее 1 мм при диаметре болтовых отверстий 18-25 мм и не более 2 мм при диаметре до 41 мм.
Фланцевые кондукторы
Для удобства установки и приварки фланцевых соединений используют специальное устройство, которое называется кондуктором. Кондуктор позволяет собирать соединения в точном соответствии с техническими условиями, указанными в чертеже.
В кондукторе для установки фланца предусмотрены универсальные приспособления, устанавливаемые на тумбах 1 и 4. Тумбу 1 перемещают по длине кондуктора в зависимости от длины собираемого изделия и крепят к раме 5 кондуктора.
Тумба 4 осуществляет возвратно-поступательное движение от цилиндра и перенастраиваемый упор для правильной настройки на полную длину собираемого элемента. Обе тумбы укомплектованы пневмоприжимами, которые прижимают фланцы к фиксаторам во время сборки. В промежутке между тумбами размещены призмы 3, регулируемые по высоте, которые служат опорами для собираемого пояса.
Сборка происходит в таком порядке: выставляют кондуктор по длине, а фиксаторы двух фланцев — на определенный радиус размещения отверстий. На стеллажах на сборочный пояс надевают фланцы. При помощи крана пояс с фланцами размещают на призмах кондуктора. После установки сборочного пояса на призмы 3 тумбу 4 перемещают до упора точной настройки.
Пояс устанавливают на одинаковом расстоянии от фиксаторов. Диски перемещают к фиксаторам и фиксируют точеными пробками (при несоответствии диаметров отверстий в фланце и фиксаторе используют переходные пробки). Затем подключают пневмоприжимы — фланец плотно прижимается к фиксатору и проводят прихватку диска к поясу. После прихватки пояс с фланцами освобождают от пневмо-прижимов и пробок; подвижную тумбу отводят назад и пояс вытаскивают портальным краном из кондуктора.
Применение приварных фланцев
Приварные фланцы широко используются в различных отраслях:
- химической промышленности;
- нефтегазовом комплексе;
- на транспорте;
- машиностроении и судостроении;
- электроэнергетике и других отраслях.
С помощью приварных фланцев происходит соединение:
- трубопроводной арматуры;
- различных резервуаров;
- приборов;
- патрубков;
- деталей машин и аппаратов.
Использование фланцевых соединений возможно в различных климатических условиях.
Контроль качества фланцевых узлов
При проверке качества фланцевых соединений возможно применение всех типов неразрушающих методов контроля:
- ультразвуковая диагностика;
- рентгенография;
- визуальный осмотр;
- дефектоскопия.
Положительные результаты достигаются и при проведении контроля в процессе сварки, соответствии расходных материалов основному металлу, использовании соответствующей сварочной проволоки.
Преимущества приварных фланцев
Фланцевые соединения представляют собой разновидность разъемного способа крепления. Применение металлических дисков позволяет, при необходимости, проводить разборку участка трубопровода для проведения регламентных работ.Сварные фланцы, в отличие от резьбовых аналогов, обеспечивают более высокую надежность соединений и являются экономически обоснованным способом присоединения труб к другим изделиям.
Установка фланцевых дисков и крепление их к трубе может осуществляться посредством:
Наиболее качественный результат обеспечивает контактная сварка. Фланцевое соединение является доступным методом монтажа. Большое разнообразие стандартов и материалов, из которых изготавливаются фланцы, позволяет подбирать оптимальные варианты для качественного разъемного соединения. Применение приварных фланцев происходит повсеместно во всех сферах промышленного производства.
Похожие статьиgoodsvarka.ru
GardenWeb
Категория: Сварочные работы
Плоские фланцы приваривают к трубам сваркой двух видов. При давлении в трубопроводе до 10 кгс/см2 фланцы приваривают без образования скоса на фланце (рис. 1, а). При давлении в трубопроводе до 25 кгс/см2 фланцы приваривают с образованием скоса на фланце, как показано на рис. 1, б.
Рис. 1. Виды приварки фланцев к трубам: а — при давлении в трубопроводе до 10 кгс/см2, б — при давлении в трубопроводе 16 и 25 кгс/см
Высота шва принимается от 5 до 10 мм, в зависимости от диаметра трубы, а расстояние от торца трубы до края фланца — на 1 мм больше.
Приваривать фланцы к патрубкам рекомендуется в приспособлении (рис. 2), предложенном инж. С. Н. Лисициным и А. Д. Бон-даренко. Приспособление состоит из нижнего неподвижного фланца 1 и верхнего 2, поворачивающегося на шарикоподшипнике.
Патрубок с прихваченным фланцем устанавливают на приспособлении, и сварщик начинает сварку. При образовании кратера он плотно опирает электрод чехольчиком обмазки в стык свариваемых деталей, держа электрод с наклоном 40—45° к горизонтальной плоскости и плавно поворачивая верхний фланец левой рукой по мере плавления электрода. Электрод остается неподвижным, а шов обрадуется при поворачивании свариваемых деталей. Сварка производится непрерывно, без обрыва дуги. Таким же способом сваривают внутренний шов.
Рис. 2. Приспособление для приварки фланцев: а — приварка наружного шва, б — приварка внутреннего шва; 1 — патрубок С нижним неподвижным фланцем, 2 — верхний вращающийся на шарикоподшипнике фланец
Сварочные работы – Приварка фланцевgardenweb.ru
Варианты приварки фланца к трубе
Фланцевое соединение довольно часто используют вместо обычной сварки, а тем более на фитинг.
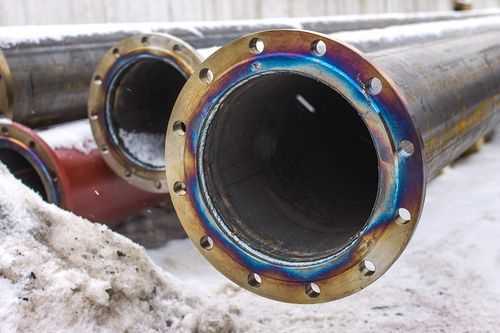
Фланцевое соединение
Фланец гарантирует не менее прочное и герметичное соединение, но при этом разъемное, чтопозволяет в любой момент демонтировать часть трубопровода для ремонта, например, или присоединения дополнительных секторов.
Классификация изделий
Общее строение детали представляет собой кольцои пластину с отверстиями по краю. Чтобы обеспечить герметичность между элементами, устанавливают еще и прокладку изрезины в соответствии с назначением трубопровода – кислотостойкой, термостойкой. Соединяют кольцо и пластину с помощью крепежа – болтов с гайками или шпилек.
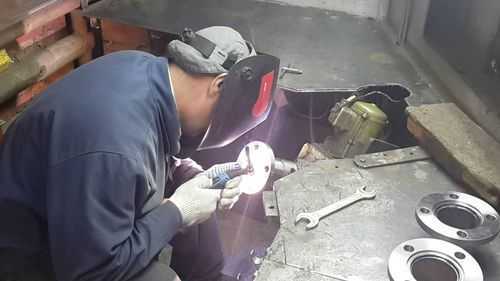
Сварка фланцев
По ГОСТ выделяют несколько разных видов фланцев. По чертежам отличия их хорошо заметны.
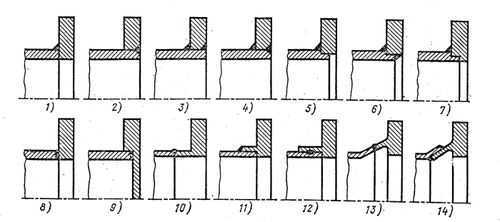
Виды сваривания фланцев
Соответственно, и приварка деталей к трубопроводу производится несколько по-разному.
- Воротниковый – характерным признаком является приварная горловина в виде конического концентратора. Такая форма позволяет более равномерно распределять давление. Воротниковая модель предназначена для коммуникаций с высоким давлением и высокой температурой носителя. Приваривается сплошным или V-швом.
- Раструбной – используется на трубах с малым диаметром, работающих под большим давлением. Минус изделия – некоторая нестойкость к коррозии. Приварка раструбной детали производится с внешней стороны угловым швом. Нужно сохранять люфт в 1,6 м, чтобы нейтрализовать эффект теплового расширения.
- Сквозной – или свободно вращающийся. Приварка сквозной трубы к фланцу по ГОСТ не производится, так как сквозной вариант применяется специально для того, чтобы деталь можно было заменить по мере необходимости. На фото – сквозное фланцевое соединение.
- Глухой – плоский диск с отверстиями. Это приспособление необходимо для заглушки концов трубопровода. Элемент неразборной, однако он только закрепляется, а не сваривается.
- Плоский – кольцо и пластина одинакового размера. Приварка плоского фланца к трубе заключается в креплении кольца, в то время как пластина остается свободного вращающейся. Он выдерживает давление до 2,5 МПа.
- Накидной – для его использования кромки труб должны быть идеально ровными, так что он не настолько универсален, как воротниковые модели. Накидной приваривается угловыми швами с внешней и с внутренней стороны.
- Резьбовый – используется на трубопроводах небольшого диаметра, где возможно сделать резьбу. Сварка при его установке используется крайне редко.
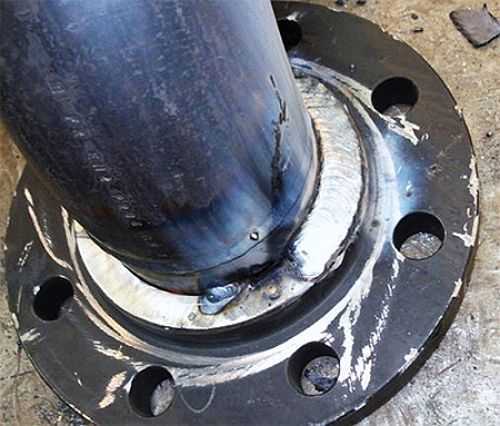
Наружняя приварка фланца
Расценки на изделия заметно отличаются. Однако стоимость переделяетсяскорее размерами пластин, а не их конструкцией, и весом, конечно же. Согласно ГОСТ изготавливаются они из углеродистой, легированной или нержавеющей стали, а такжековкого чугуна. Расценки на металл и определяют стоимость приспособлений.
Технология сварки в принципе одинакова, за исключением крепления патрубков. Однако необходимо учитывать и сложность конструкции – рекомендуется уточнять чертежи, и соответствие требованиям по креплению.
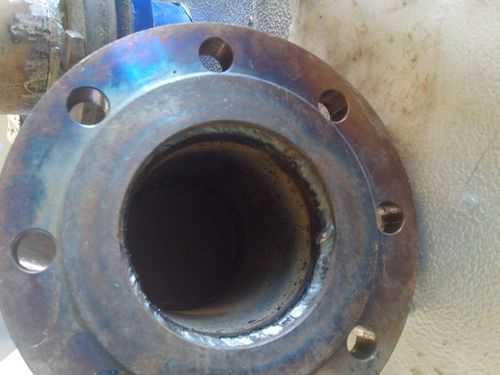
Внутренняя приварка фланца
В большинстве случаев необходимо сохранение зазора в стыке. Если люфт не нужен, допускается техника сварки в лодочку. Если люфт должен быть большим – более 4–5 мм, изделие приваривают угловыми швами. Все это, естественно, влияет на расценки.
Размеры шва зависят от трубопровода. Ширина внутреннего шва обычно равна толщине стенки, высота – от 0,5 до 1 см, что определяется сечением трубопровода. Внешний шов требует большего наплавления металла, поэтому он несколько несимметричен.
Приварка производится с 2 сторон: сначала с наружной, а затем, для уплотнения шва – с внутренней. Такой метод более всего подходит для плоских фланцевых деталей. Сварка с одной стороны осуществляется, если изделие приваривается встык, как в случае с воротниковым фланцем.
Приспособление для приварки фланцев к трубам подходит не всякое. Обычно рекомендуется аппарат Лисицына и Бондаренко. При сварке электрод здесь остается неподвижным, а проворачивается трубопровод.
На видео процесс сварки рассматривается более подробно.
trubygid.ru
www.samsvar.ru
Варианты приварки фланца к трубе — Море задвижек
Фланцевое соединение довольно часто используют вместо обычной сварки, а тем более на фитинг.
Фланцевое соединение
Фланец гарантирует не менее прочное и герметичное соединение, но при этом разъемное, чтопозволяет в любой момент демонтировать часть трубопровода для ремонта, например, или присоединения дополнительных секторов.
Классификация изделий
Общее строение детали представляет собой кольцои пластину с отверстиями по краю. Чтобы обеспечить герметичность между элементами, устанавливают еще и прокладку изрезины в соответствии с назначением трубопровода – кислотостойкой, термостойкой. Соединяют кольцо и пластину с помощью крепежа – болтов с гайками или шпилек.
Сварка фланцев
По ГОСТ выделяют несколько разных видов фланцев. По чертежам отличия их хорошо заметны.
Виды сваривания фланцев
Соответственно, и приварка деталей к трубопроводу производится несколько по-разному.
- Воротниковый – характерным признаком является приварная горловина в виде конического концентратора. Такая форма позволяет более равномерно распределять давление. Воротниковая модель предназначена для коммуникаций с высоким давлением и высокой температурой носителя. Приваривается сплошным или V-швом.
- Раструбной – используется на трубах с малым диаметром, работающих под большим давлением. Минус изделия – некоторая нестойкость к коррозии. Приварка раструбной детали производится с внешней стороны угловым швом. Нужно сохранять люфт в 1,6 м, чтобы нейтрализовать эффект теплового расширения.
- Сквозной – или свободно вращающийся. Приварка сквозной трубы к фланцу по ГОСТ не производится, так как сквозной вариант применяется специально для того, чтобы деталь можно было заменить по мере необходимости. На фото – сквозное фланцевое соединение.
- Глухой – плоский диск с отверстиями. Это приспособление необходимо для заглушки концов трубопровода. Элемент неразборной, однако он только закрепляется, а не сваривается.
- Плоский – кольцо и пластина одинакового размера. Приварка плоского фланца к трубе заключается в креплении кольца, в то время как пластина остается свободного вращающейся. Он выдерживает давление до 2,5 МПа.
- Накидной – для его использования кромки труб должны быть идеально ровными, так что он не настолько универсален, как воротниковые модели. Накидной приваривается угловыми швами с внешней и с внутренней стороны.
- Резьбовый – используется на трубопроводах небольшого диаметра, где возможно сделать резьбу. Сварка при его установке используется крайне редко.
Наружняя приварка фланца
Расценки на изделия заметно отличаются. Однако стоимость переделяетсяскорее размерами пластин, а не их конструкцией, и весом, конечно же. Согласно ГОСТ изготавливаются они из углеродистой, легированной или нержавеющей стали, а такжековкого чугуна. Расценки на металл и определяют стоимость приспособлений.
Приварка фланца к трубе по ГОСТ
Технология сварки в принципе одинакова, за исключением крепления патрубков. Однако необходимо учитывать и сложность конструкции – рекомендуется уточнять чертежи, и соответствие требованиям по креплению.
Внутренняя приварка фланца
В большинстве случаев необходимо сохранение зазора в стыке. Если люфт не нужен, допускается техника сварки в лодочку. Если люфт должен быть большим – более 4–5 мм, изделие приваривают угловыми швами. Все это, естественно, влияет на расценки.
Размеры шва зависят от трубопровода. Ширина внутреннего шва обычно равна толщине стенки, высота – от 0,5 до 1 см, что определяется сечением трубопровода. Внешний шов требует большего наплавления металла, поэтому он несколько несимметричен.
Приварка производится с 2 сторон: сначала с наружной, а затем, для уплотнения шва – с внутренней. Такой метод более всего подходит для плоских фланцевых деталей. Сварка с одной стороны осуществляется, если изделие приваривается встык, как в случае с воротниковым фланцем.
Источник: trubygid.ru
Остались вопросы?Наши менеджеры помогут Вам!Звоните по телефону 8-343-286-17-65, либо пишите на электронную почту — [email protected].
prz-ekb.ru
7.5. Приварка фланцев, арматуры и других деталей к трубам
7.5.1. Арматуру (клапаны, задвижки), фланцы, донышки, заглушки и другие фасонные детали, присоединяемые к трубам стыковым сварным швом, приваривают с соблюдением тех же режимов и технологии, что и при сварке стыков трубопровода соответствующих диаметра и марки стали, а также требований п.3.7иподразделов 6.4и6.5.
7.5.2. Плоские фланцы на давление Р <= 2,5 Мпа (25 кгс/см2) для диаметра труб 600 мм и более изготавливаются по ОСТ 34 10.755-97. Фланец приваривается к трубе двумя угловыми швами – наружным и внутренним (рис.7.18). Сначала накладывают наружный шов, затем – внутренний. Размеры швов приварки указаны втабл.7.2. Внутренний шов, являющийся лишь уплотняющим, имеет катет 7(-2) мм независимо от толщины стенки трубы.
Для труб диаметром менее 600 мм плоские приварные фланцы изготавливаются по ГОСТ 12820 и размеры катетов шва указываются в конструкторской документации.
“Рис.7.18. Приварка плоских фланцев к трубе”
7.5.3. Приварку креплений из высоколегированных сталей к трубам пароперегревателя и другим элементам котла, находящимся в зонах высоких температур, а также приварку к паропроводам реперов для измерения ползучести необходимо выполнять аустенитными электродами диаметром не более 3 мм на режимах с минимальным тепловложением. Марка электродов выбирается по данным табл.4.2. Ток устанавливается из расчета 25-30 А на 1 мм диаметра электрода. Сварку следует вести короткой дугой с незначительными колебательными движениями электрода. Каждый следующий валик необходимо накладывать только после снижения температуры металла в зоне сварки ниже 100°С. Термическая обработка таких сварных соединений не производится.
7.5.4. К трубам из углеродистых и низколегированных теплоустойчивых и конструкционных сталей упоры, накладки, подвески и другие детали креплений из таких же сталей следует приваривать сплошным угловым швом с катетом, указанным в рабочих чертежах, с использованием электродов, подбираемых по данным табл.4.1. Диаметр электродов должен быть не более 3 мм. Если детали креплений и трубы изготовлены из стали разных марок одного структурного класса, электроды нужно выбирать по менее легированной стали.
Таблица 7.2
Размеры швов приварки плоских фланцев (ост 34 10.755-97)
┌──────────┬───────┬─────────────┬─────────────┬───────────┬─────────────┐
│ Условное │Услов- │ Размеры │ Зазор между │ Глубина │ Размер │
│ давление │ ный │присоединяе- │ трубой и │ фаски на │катетов шва, │
│ Р_у, МПа │проход │мых труб Д_н │ фланцем а, │ фланце с │ мм │
│(кгс/см2) │Д_у, мм│ х S, мм │мм, не более │ +-1, мм │ │
│ │ │ │ │ ├──────┬──────┤
│ │ │ │ │ │ К │ К_2 │
├──────────┼───────┼─────────────┼─────────────┼───────────┼──────┼──────┤
│ │ 600 │ 630×12 │ │ 12 │ 12 │ 22 │
│ │ │ │ │ │ (+3) │ (+5) │
│ │ │ │ │ │ │ │
│ │ 700 │ 720×9 │ │ 9 │9 (+3)│ 18 │
│ │ │ │ │ │ │ (+5) │
│ │ │ │ │ │ │ │
│ 2,5 (25) │ 800 │ 820х11 │ 1,5 │ 11 │ 11 │ 21 │
│ │ │ │ │ │ (+3) │ (+5) │
│ │ │ │ │ │ │ │
│ │ 1000 │ 1020×14 │ │ 14 │ 14 │ 26 │
│ │ │ │ │ │ (+5) │ (+5) │
│ │ │ │ │ │ │ │
│ │ 1200 │ 1220×14 │ │ 14 │ 14 │ 26 │
│ │ │ │ │ │ (+5) │ (+5) │
├──────────┼───────┼─────────────┼─────────────┼───────────┼──────┼──────┤
│ │ 700 │ 720×9 │ │ 9 │9 (+3)│ 18 │
│ │ │ │ │ │ │ (+5) │
│ │ │ │ │ │ │ │
│ │ 800 │ 820×9 │ │ 9 │9 (+3)│ 18 │
│ │ │ │ │ │ │ (+5) │
│ │ │ │ │ │ │ │
│ 1,6(16) │ 1000 │ 1020×10 │ 1,5 │ 10 │ 10 │ 20 │
│ │ │ │ │ │ (+3) │ (+5) │
│ │ │ │ │ │ │ │
│ │ 1200 │ 1220×11 │ │ 11 │ 11 │ 20 │
│ │ │ │ │ │ (+3) │ (+5) │
│ │ │ │ │ │ │ │
│ │ 1400 │ 1420×14 │ │ 14 │ 14 │ 26 │
│ │ │ │ │ │ (+5) │ (+5) │
│ │ │ │ │ │ │ │
│ │ 1600 │ 1620×14 │ │ 14 │ 14 │ 26 │
│ │ │ │ │ │ (+5) │ (+5) │
├──────────┼───────┼─────────────┼─────────────┼───────────┼──────┼──────┤
│ │ 700 │ 720×9 │ │ 9 │9 (+3)│ 18 │
│ │ │ │ │ │ │ (+5) │
│ │ │ │ │ │ │ │
│ │ 800 │ 820×9 │ │ 9 │9 (+3)│ 18 │
│ │ │ │ │ │ │ (+5) │
│ │ │ │ │ │ │ │
│ 1,0(10) │ 1000 │ 1020×10 │ 1,5 │ 10 │ 10 │ 20 │
│ │ │ │ │ │ (+3) │ (+5) │
│ │ │ │ │ │ │ │
│ │ 1200 │ 1220×11 │ │ 11 │ 11 │ 21 │
│ │ │ │ │ │ (+3) │ (+5) │
│ │ │ │ │ │ │ │
│ │ 1400 │ 1420×14 │ │ 14 │ 14 │ 26 │
│ │ │ │ │ │ (+5) │ (+5) │
│ │ │ │ │ │ │ │
│ │ 1600 │ 1620×14 │ │ 14 │ 14 │ 26 │
│ │ │ │ │ │ (+5) │ (+5) │
├──────────┼───────┼─────────────┼─────────────┼───────────┼──────┼──────┤
│ │ 1200 │ 1220×14 │ │ 11 │ 11 │ 21 │
│ │ │ │ │ │ (+3) │ (+5) │
│ │ │ │ │ │ │ │
│ 0,6 (6) │ 1400 │ 1420×14 │ 1,5 │ 14 │ 14 │ 26 │
│ │ │ │ │ │ (+5) │ (+5) │
│ │ │ │ │ │ │ │
│ │ 1600 │ 1620×14 │ │ 14 │ 14 │ 26 │
│ │ │ │ │ │ (+5) │ (+5) │
└──────────┴───────┴─────────────┴─────────────┴───────────┴──────┴──────┘
Подогрев при приварке деталей креплений к трубам из углеродистых и низколегированных сталей осуществляется в соответствии с рекомендациями, приведенными в табл.6.3, при этом за толщину свариваемых деталей принимается толщина трубы. Подогрев трубы и детали осуществляется в районе приварки.
Приварка упоров к трубопроводам из низколегированных теплоустойчивых сталей должна выполняться по одной из схем, приведенных на рис.7.19. В случае приварки упора двумя фланговыми швами (рис.7.19, а) каждый слой сваривается в направлении, противоположном направлению сварки предыдущего слоя. В случае приварки упора двумя фланговыми и одним лобовым швами (рис.7.19, б) сварка начинается в середине лобового шва (в точке Б) и ведется до конца правого или левого флангового шва. Если длина шва от точки Б до конца флангового шва более 250 мм, то сварка должна выполняться обратноступенчатым способом. Приварку упора к трубе диаметром более 500 мм должны выполнять одновременно два сварщика.
Условия, при которых необходима термообработка угловых швов приварки деталей креплений к трубам, и режим термообработки указаны в подразделе 17.2.
Сварные соединения деталей креплений из углеродистой стали с трубами из низколегированной стали термической обработке не подвергаются.
7.5.5. Приварка бобышек для термопар к трубопроводам производится электродами диаметром не более 3 мм. Марка электродов выбирается по данным табл.4.1.
Необходимость и режим предварительного подогрева определяются по данным табл.6.3ип.6.4.1. При приварке бобышек к трубопроводу диаметром менее 219 мм необходим предварительный подогрев бобышек и трубы по всему периметру, при диаметре трубопровода 219 мм и более подогревается труба только в районе приварки бобышек и сама бобышка.
Необходимость и режим термообработки этих сварных соединений указаны в подразделе 17.2.
“Рис.7.19. Схемы приварки упора к трубопроводу двумя фланговыми швами (а), двумя фланговыми и одним лобовым швами (б)”
studfiles.net
СТ ЦКБА 013-2007 Арматура трубопроводная. Приварка арматуры к трубопроводу. Технические требования
Технический комитет по стандартизации
«Трубопроводная арматура и сильфоны»
(ТК 259)
Закрытое акционерное общество «Научно-производственная фирма
«Центральное конструкторское бюро арматуростроения»
СТАНДАРТ ЦКБА
СТ ЦКБА 013-2007
Арматура трубопроводная
ПРИВАРКА АРМАТУРЫ К ТРУБОПРОВОДУ
Технические требования
НПФ «ЦКБА»
2007
Предисловие
1 РАЗРАБОТАН Закрытым акционерным обществом «Научно-производственная фирма «Центральное конструкторское бюро арматуростроения» (ЗАО «НПФ «ЦКБА»).
2 УТВЕРЖДЕН И ВВЕДЕН В ДЕЙСТВИЕ Приказом от 27.09.2007 г. № 53.
3 СОГЛАСОВАН:
Техническим комитетом по стандартизации «Трубопроводная арматура и сильфоны» (ТК 259).
4 ВЗАМЕН РД 24.207.02-90 «Приварка арматуры к трубопроводу. Технические требования».
5 ПЕРЕИЗДАНИЕ с учетом изменения № 1 (2014 г.)
СОДЕРЖАНИЕ
СТАНДАРТ ЦКБА
Арматура трубопроводная ПРИВАРКА АРМАТУРЫ К ТРУБОПРОВОДУТехнические требования |
Дата введения – 01.01.2008
Стандарт распространяется на трубопроводную арматуру на номинальное давление до PN 200 (20,0 МПа) и DN от 10 до DN 1600 включительно и устанавливает конструктивные элементы разделки кромок, требования к подготовке кромок, требования к контролю кромок под сварку литых деталей, методы контроля и оценку дефектов, а также основные технологические мероприятия по приварке трубопроводной арматуры к трубопроводу и переходников (катушек) к арматуре и трубопроводу.
(Измененная редакция. Изм. № 1)
В настоящем стандарте использованы нормативные ссылки на следующие межгосударственные стандарты и нормативные документы:
ГОСТ 7512-82 Контроль неразрушающий. Соединения сварные. Радиографический метод
ГОСТ 9941-81 Трубы бесшовные холодно- и теплодеформированные из коррозионно-стойкой стали. Технические условия
ГОСТ 18442-80 Контроль неразрушающий. Капиллярные методы. Общие требования
ГОСТ 23055-78 Контроль неразрушающий. Сварка металлов плавлением. Классификация сварных соединений по результатам радиографического контроля
ГОСТ Р 52079-2003 Трубы стальные сварные для магистральных газопроводов, нефтепроводов и нефтепродуктопроводов. Технические условия
РД 5Р.9537-80 Контроль неразрушающий. Полуфабрикаты и конструкции металлические. Капиллярные методы и средства контроля качества поверхности
РД 25.160.00-КТН-011-10 Сварка при строительстве и капитальном ремонте магистральных нефтепроводов
СТ ЦКБА 025-2006 Арматура трубопроводная. Сварка и контроль качества сварных соединений. Технические требования
ТУ 14-3-197-89 Трубы бесшовные из коррозионностойких марок стали с повышенным качеством поверхности. Технические требования
ТУ 14-3-1573-96 Трубы стальные сварные прямошовные диаметром 530 – 1020 мм с толщиной стенки до 32 мм для магистральных газопроводов, нефтепроводов и нефтепродуктопроводов
ТУ 14-3-1698-2000 Трубы стальные электросварные прямошовные диаметром 1020, 1220 мм для газонефтепроводов. Технические условия
ТУ 14-3-1973-98 Трубы стальные электросварные спиральношовные из низколегированной стали с наружным антикоррозионным покрытием для сооружения магистральных нефтепроводов
ТУ У27.2-00191135-010:2005 Трубы стальные электросварные прямошовные экспандированные D 1067 и 1220 мм из стали класса прочности К56 и К60 для магистрального нефтепровода «Восточная Сибирь – Тихий океан».
(Измененная редакция. Изм. № 1)
3.1 Конструктивные элементы разделки кромок патрубков, ответных фланцев трубопроводной арматуры, переходников указаны в таблице 1.
Таблица 1
Условное обозначение |
Конструктивные элементы приварки арматуры к трубопроводу |
Толщина стенки арматуры S, мм |
Дополнительные указания |
С1 |
До 2,0 включ. |
До 5 мм включительно может производиться калибровка (раздача) концов трубопровода |
|
С2 |
Св. 2,0 до 3,0 включ. |
||
C3 |
Свыше 3,0 |
||
C4 |
Свыше 16,0 |
Применяется по согласованию с заказчиком |
|
C5 |
|||
С6 (Тип 1) |
До 15 включ. |
Наружный и внутренний диаметры арматуры соответствуют диаметрам трубопровода |
|
С7 (Тип 2) |
Свыше 15 |
||
С8 (Тип 3) |
До 15 включ. |
Если внутренний диаметр арматуры отличается от диаметра трубопровода, то производится расточка по внутреннему диаметру. Остальные элементы разделки по С6 |
|
С9 (Тип 4) |
Свыше 15 |
Если внутренний диаметр арматуры отличается от диаметра трубопровода, то производится расточка по внутреннему диаметру |
|
C10 (Тип 5) |
До 15 включ. |
Если внутренний и наружный диаметры арматуры отличается от диаметра трубопровода, то производится расточка как по внутреннему, так и по наружному диаметру |
|
С11 (Тип 6) |
Свыше 15 |
||
Примечания: 1 а – размер для присоединения трубы или переходного кольца, мм; S – толщина стенки трубопровода; С – ширина кольцевого притупления; В – высота фаски. 2 B = 9 мм при 15 < S ≤ 19 мм; В = 10 мм при 19 < S ≤ 22 мм; В = 12 мм при S > 22. 3 С = (1,8 ± 0,8) мм 4 При применении подкладных колец по п. 3.3 разделки необходимо доработать в соответствии с рисунками 1 и 2. |
3.2 Разделка кромок арматуры, переходников (катушек) для приварки к трубопроводу должна быть указана заказчиком и аналогична разделке трубопровода. В приложении А приведены стандарты на трубы, допускается использование других стандартов. При этом заказчиком должны быть указаны размеры труб – максимальный и минимальный внутренний диаметр и толщина стенки или принятый диаметр расточки (DP). В случае отсутствия вышеперечисленных данных диаметр расточки (DP) рекомендуется определять по формуле:
DP = (D + 1,6) мм,
где D – максимальный внутренний диаметр трубы по НД на поставку.
3.3 Сварка арматуры с трубопроводом и с переходниками (катушками) может производиться для всех указанных в таблице 1 сварных соединений без подкладных колец «на весу» или на остающихся подкладных кольцах как на цилиндрических, так и на конических, если нет специальных указаний заказчика о недопустимости их применения, нет ограничений по среде или другим признакам.
Форма и размеры рекомендуемых цилиндрических и конических подкладных колец указаны на рисунках 1 и 2.
Рисунок 1 Цилиндрическое подкладное кольцо |
Рисунок 2 Коническое подкладное кольцо |
Материал подкладного кольца должен соответствовать материалу трубопровода или марки материала конца присоединяемой арматуры или переходника (катушки).
При сварке из сталей перлитного класса различных марок подкладное кольцо изготавливается из менее легированной стали.
3.4 Длина переходника (катушки) l определяется в зависимости от наружного диаметра арматуры (D0) (рисунок 3):
– при D0 > 100 мм l ³ 100 мм
– при D0 ≤ 100 мм l не менее D0, с учетом доступности контроля ультразвуковым методом и радиографическим.
Допускаются другие размеры по указанию заказчика или исходя из конструктивной необходимости.
Рисунок 3
3.5 Допускается смещение внутренних кромок патрубка арматуры и трубы при сборке под сварку согласно таблице 2.
Таблица 2
Толщина стенки S, мм |
Максимальное допустимое смещение внутренних кромок, мм |
До 3 |
0,20S |
Св. 3 до 6 |
0,10S + 0,3 |
Св. 6 до 10 |
0,15S |
Св. 10 до 20 |
0,05S + 1,0 |
Св. 20 |
0,10S (но не более 3 мм) |
Примечание – При смещении более указанного в таблице 2 производится раздача или расточка трубы под углом (10 ± 30) °С или по разделке патрубка, фланца и т.д., т.е. ответной детали.
3.6 Если номинальная толщина стенки концов арматуры по наружному диаметру превышает не более чем на 30 % толщину стенки трубопровода и не превышает 5 мм, то допускается применять сварные соединения без утонения стенки арматуры, причем наклон поверхности шва должен обеспечить плавный переход от арматуры к трубопроводу.
3.7 При разности в толщине свариваемых деталей свыше значений, указанных в п. 3.6 настоящего стандарта (п. 3.6 не относится к разделкам С10, С11 – см. таблицу 1), на конце разделки арматуры, имеющей большую толщину по наружному диаметру, должен быть сделан скос до расчетной толщины, как указано на рисунке 4.
Рисунок 4
3.8 При сварке арматуры с трубопроводом из разнородных марок сталей, необходимо предусмотреть проектантом в заводских условиях приварку переходников к арматуре из стали идентичной марке стали трубопровода или стали того же класса, которая приваривается к трубопроводу без подогрева и последующей термообработки.
Допускается по согласованию с заказчиком не приваривать переходники.
3.9 По требованию заказчика допускаются другие разделки с соблюдением требований настоящего стандарта.
4.1 Подготовка кромок патрубков, фланцев под сварку арматуры к трубопроводу, изготовленной из поковок, штамповок, труб, сортового проката и литья должна выполняться механическим способом. При этом необходимо внутреннюю и наружную поверхности механически обработать или зачистить до чистого металла с шероховатостью не более Ra = 12,5 на ширину не менее 20 мм от границы разделки кромки или с другой чистотой поверхности согласно НД на конкретные указанные методы контроля.
Радиографический контроль кромок литья должен производиться после механической обработки или зачистки литой детали (шероховатость поверхности должна быть в соответствии с требованиями чертежа) перед разделкой кромки под сварку или после разделки с применением компенсационных колец или планок.
4.2 Кромки литых деталей, подлежащих приварке к трубопроводу, на участке шириной L от торца кромки по всему периметру (см. рисунок 5) должны быть перед сваркой проконтролированы методами, согласно п. 13.2 СТ ЦКБА 025 и указанными в КД, из числа ниже перечисленных:
– визуальным и измерительным контролем, который проводится невооруженным глазом, а в сомнительных случаях при помощи лупы от четырехкратного до семикратного увеличения;
– капиллярным контролем;
– радиографическим контролем;
– ультразвуковой дефектоскопией.
При этом необходимо предусмотреть величину околошовной зоны для радиографического контроля, которая указана по ГОСТ 7512 п. 5.7. и составляет при толщине свариваемых кромок:
а) до 5 мм – не менее 5 мм;
б) свыше 5 мм до 20 мм – не менее толщины свариваемых кромок;
в) свыше 20 мм – не менее 20 мм.
Разрешается уменьшение величины L, если прямой участок имеет ограниченную длину или по другим причинам.
Рисунок 5
4.3 Дефекты, выявленные в кромках под сварку визуальным контролем, капиллярной дефектоскопией, радиографическим контролем, ультразвуковой дефектоскопией на участке шириной L не должны превышать норм СТ ЦКБА 025.
Оценка дефектов может производиться по другим НД или другим нормам, указанным в КД.
4.4 Обязательным является визуальный контроль.
При визуальном контроле дефекты не допускаются.
4.5 Капиллярный контроль кромок литых деталей производится по III классу РД 5Р.9537 или ГОСТ 18442.
Дефекты не допускаются.
4.6 При давлении выше 6,3 МПа (63 кгс/см2), если условия работы отличаются от указанных в разделе 13.2 СТ ЦКБА 025 или согласно указанию КД, металл на участке L (рисунок 4) необходимо проконтролировать радиографическим или ультразвуковым (УЗК) методами контроля.
4.7 При радиографическом контроле, если нет указаний в КД, допускаются дефекты по VII классу дефектности по ГОСТ 23055.
(Измененная редакция. Изм. № 1)
4.8 Концы патрубков литой арматуры под приварку по результатам УЗК, если нет указаний в КД, должны удовлетворять следующим показателям:
– фиксации подлежат дефекты с эквивалентной площадью S0 = 30 мм2;
– не допускаются дефекты площадью S1 > 60 мм2;
– суммарное количество дефектов на участке длиной 100 мм не должно превышать:
– для стенки толщиной 20 – 25 мм – 3 шт.;
– 26 – 34 мм – 4 шт;
– 35 – 65 мм – 5 шт.
при минимальном условном расстоянии между дефектами 10 мм.
Не допускаются протяженные дефекты с условной протяженностью, превышающей протяженность контрольного отражателя S1 = 60 мм2.
4.9 Результаты радиографического и ультразвукового контроля с указанием размеров и расположения дефектов должны быть указаны в документации, передаваемой заказчику, и при оценке качества сварного соединения не учитываются.
4.10 Недопустимые дефекты, обнаруженные при контроле металла литья на участке L (рисунок 4) методами согласно КД, необходимо удалить и произвести заварку по технологической документации (инструкции, типового техпроцесса и т.д.).
4.11 При обнаружении трещин, с целью определения полноты удаления их, выборку под заварку рекомендуется подвергнуть капиллярному контролю или магнитопорошковой дефектоскопии, или местному травлению 15 % раствором азотной кислоты в спирте.
4.12 В случае большого объема исправления дефектов кромок литой арматуры проектантом совместно со специалистами по литью и сварке предприятия-изготовителя арматуры решается вопрос о целесообразности применения переходников (из трубы, сортового проката и т.д.) из стали идентичной (или того же класса) марки стали трубопровода, или о наплавке кромок, или другим способом, обеспечивающим качество металла, подлежащего приварке к трубопроводу.
5.1 Приварка арматуры к переходникам (катушкам) в заводских условиях, а также контроль качества сварных соединений должны производиться по СТ ЦКБА 025.
По требованию заказчика для переходников и их приварки к трубопроводам могут быть использованы другие конструкционные и сварочные материалы, не указанные в СТ ЦКБА 025. При этом технология выполнения сварки и контроль качества производится по СТ ЦКБА 025 с дополнительными требованиями заказчика или по НД заказчика.
Для магистральных нефтепроводов сварка производится по РД 25.160.00-КТН-011-10.
(Измененная редакция. Изм. № 1)
5.2 При приварке арматуры к трубопроводу необходимо предохранять от нагрева, если указано в ТУ или КД, внутренние детали с учетом температуры их применения.
Для этого необходимо зону, прилегающую ко шву (или контролируемую зону) со стороны арматуры, закрыть мокрой бязью или мокрым асбестом (постоянно их охлаждая в холодной воде), сухими медными теплоотводами или сухим льдом или другими способами, а сварку производить с охлаждением каждого валика (после каждого прохода) до остывания металла в зоне возобновления сварки не выше 100 °С.
Кроме этого, необходимо контролировать температуру нагрева в контролируемой зоне, точки измерения температуры устанавливаются ПТД.
5.3 При сварке арматуры с трубопроводом или арматуры с переходниками или переходников с трубопроводом в случае необходимой зачистки концов разделки по внутренней и наружной поверхностям или доработки разделки, или зачистки корня шва при приварке переходника и т.д. необходимо защитить внутреннюю поверхность арматуры от попадания грата, пыли и др. загрязнений.
Для этого рекомендуется закрыть внутреннюю поверхность арматуры или переходника любым доступным способом (заглушки, ткань и пр.).
(справочное)
Перечень стандартов на трубы
Таблица А.1 – Перечень стандартов на трубы
НД |
Марка стали |
Категория прочности (КП или К) |
Диаметр (D) и толщина (S), мм |
ГОСТ 9941-81 Трубы бесшовные холодно- и теплодеформированные из коррозионностойкой стали. Технические условия |
12Х18Н10Т, |
По требованию потребителя |
D от 5 до 273 |
08Х18Н10Т, |
S от 0,2 до 22 |
||
10Х17Н13М2Т |
|||
ГОСТ Р 52079-2003 Трубы сварные стальные для магистральных газопроводов, нефтепроводов и нефтепродуктопроводов |
Не указано |
К34, К38, К42, |
D от 114 до 1420 |
К48, К50, К52, |
S от 3 до 40 |
||
К54, К55, К56, |
|
||
К60 |
|
||
sт/sв ≤ 0,9 |
|
||
ТУ 14-3-197-89 Трубы бесшовные из коррозионностойких марок стали с повышенным качеством поверхности |
08Х18Н10Т |
sв³ 50 |
D от 6 до 325 |
S от 6 до 12 |
|||
ТУ 14-3-1573-96 Трубы стальные электросварные прямошовные диаметром 530 - 1020 мм с толщиной стенки до 32 мм для магистральных газопроводов, нефтепроводов и нефтепродуктопроводов. |
12Г2С, 09Г2С и др. |
К50, К52, К54, |
D от 530 до 1020 |
К55, К56, К60 |
S до 32 мм |
||
ТУ 14-3-1698-2000 Трубы стальные электросварные прямошовные |
13ГС, 13ГСУ, |
К52 |
D 1020, 1120 |
12ГСБ, 09ГСФ, |
S от 10 до 16 |
||
10ГНБ |
|||
13Г1С-У |
КП55 |
||
12Г2СБ |
К56 |
||
09ГНФБ |
|||
08Г1НФБ |
К60 |
||
ТУ 14-3-1973-98 Трубы стальные электросварные спиральношовные из низколегированной стали с наружным покрытием для сооружения магистральных нефтепроводов |
17Г1С, |
К56, К60, Х70 |
D 530, 630, 720, |
10Г2ФБ, 20 |
820, 1020, 1120 |
||
|
S от 7 до 14 |
||
|
|||
ТУ У 27.2-00191135-010:2005 Трубы стальные электросварные прямошовные экспандированные D 1067 и 1220 мм из стали класса прочности К56 и К60 для магистрального нефтепровода «Восточная Сибирь – Тихий океан» |
Не указано |
КП56 |
D 1067, 1220 |
КП60 |
S от 11 до 27 |
(Измененная редакция. Изм. № 1)
Лист регистрации изменений
Изм. |
Номера листов (страниц) |
Всего листов (страниц) в документе |
№ документа |
Входящий № сопроводительного документа и дата |
Подпись |
Дата |
|||
измененных |
замененных |
новых |
аннулированных |
||||||
1 |
14, 16 |
3, 4, 5, 17 |
– |
– |
19 |
Изм. 1 |
Пр. № 79 25.11.14 |
01.12.2014 |
Генеральный
директор |
_______________ подпись |
Дыдычкин В.П. |
Первый
заместитель |
_______________ подпись |
Тарасьев Ю.И. |
Заместитель
генерального директора – |
_______________ подпись |
Ширяев В.В. |
Зам.
главного конструктора – |
_______________ подпись |
Дунаевский С.Н. |
|
|
|
Исполнители: |
|
|
Руководитель подразделения |
_______________ подпись |
Журкович Т.Е. |
Ведущий специалист по сварке |
_______________ подпись |
Сергеева Г.А. |
Инженер-металловед |
_______________ подпись |
Мулекова А.А. |
|
|
|
Согласовано: |
|
|
Председатель ТК 259 |
_______________ подпись |
Власов М.И. |
files.stroyinf.ru